‘In-house all Processes’ Including Special Processes.
SHEET METAL FORMING
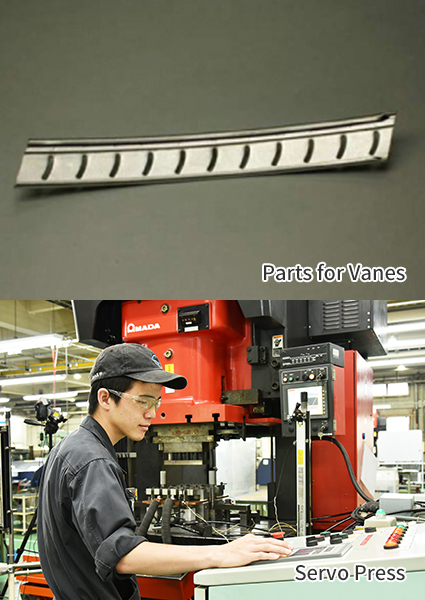
Press Forming
< Overview of Process >
Crank Press, Horn Press, Hydraulic Press, Turret Punch Press, Servo Press and other press types, Precision Bending using Press Brake, Spinning, NC Spinning, Expanding
“Sheet Metal Forming” is our core technology. Our company has continuously created various works out of individual sheet metals. Nowadays, there are many jet engines and space equipment using our parts to which the Yoshimasu sheet Metal Forming technique is applied. Our company is capable of designing metallic mold dies that support our press machines, and has a lot of accumulated data such as spring-back changes, drawing ratios, bending radiuses etc. related to hard-to-form materials used in the industry. In addition, our turret press forming made it possible to make φ0.5 holes using an ultra-thin metal dies.
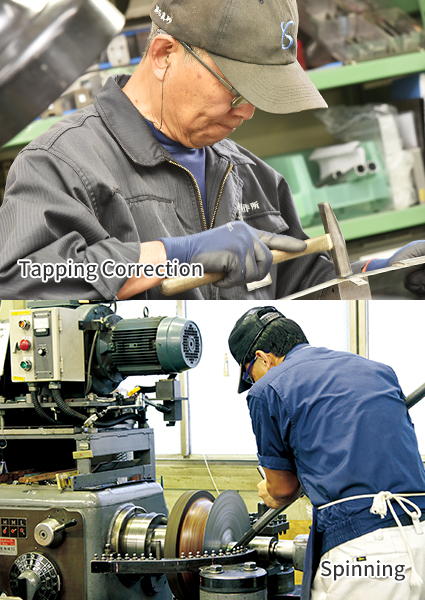
Sheet Metal Forming
< Overview of Process >
Cutting, Rolling, Expanding, Spinning, and Tapping Correction of Nickel and Titanium Alloy Sheet Metals. Precise Press Brake Bending, Spinning, NC Spinning, Tapping Correction and Welding.
< Product Example >
Thin ring-shaped parts available for rotary machines such as jet engines.
Precision sheet metal forming for manufacturing thin parts (ex. aerofoils) that have complicated shapes and are used at high temperature.
The hard to form materials used in the industry have different mechanical properties between lots, which is dealt with the experiences and skills we have gained. Our company also has a traditional corporate culture of human resource training, where skilled workers train younger workers.
MACHINING
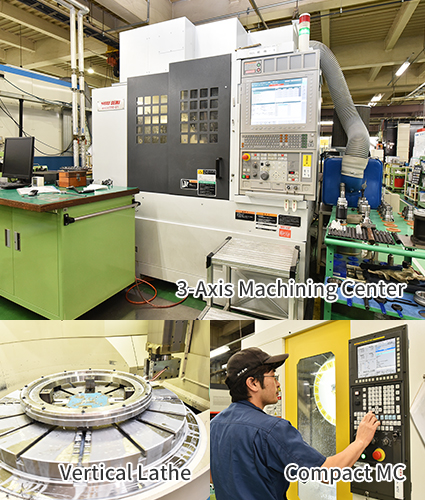
Machining
< Overview of Process >
Machining (lathing and milling) not only for detail parts, also for jointed or fabricated weldments, etc.
Trimming for press formed sheet metal parts available for rotary machines such as jet engines, and lathing for structural weldments. Our company also produces metallic mold dies used in our own plants.
SPECIAL PROCESS
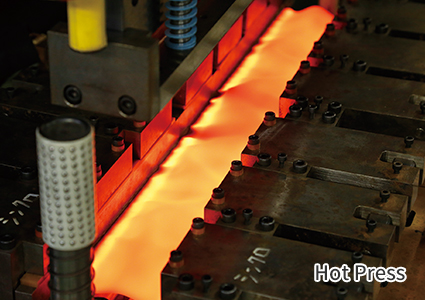
Hot Press
Based on our long experience in hot forming for titanium, in 2014, Our company developed a new method, electrical resistance heating hot-stamping, with a laboratory in a university, and the method makes the forming time short.
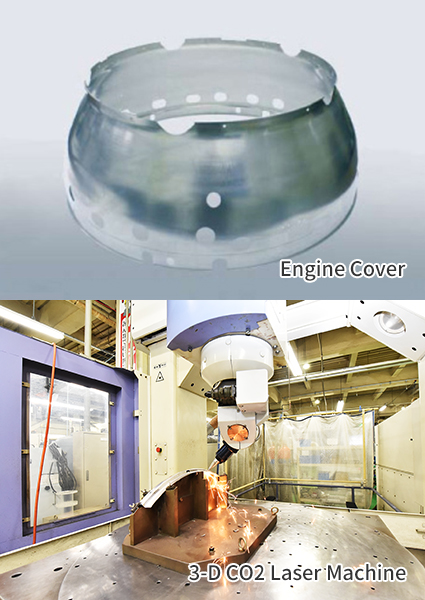
Laser Machining
< Overview of Process >
Cutting and Drilling for 3-D shapes, using NC controlled Fiber Laser, CO2, or YAG Laser
The laser machining process has NADCAP accreditation. Thickness of heat affected layers (: recast layers formed on surfaces in electric machining processes) are controlled to ensure the processes are in high-quality.
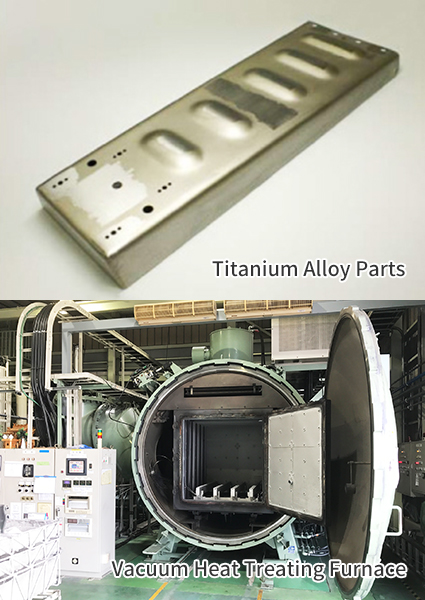
Heat Treatment
< Overview of Process >
Inter-process heat treatment to relieve work-hardening that arises in other plastic forming processing such as vacuum heat treatment after press forming; stress relief after welding; and stress relief, solutionizing and/or aging treatment of nickel, stainless and titanium alloys.
Brazing in vacuum furnaces with nickel brazing materials
The heat treatment process has NADCAP accreditation.
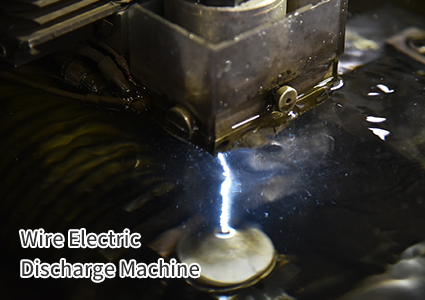
Wire Electric Discharge Machining
The wire electric discharge machining has NADCAP accreditation. The wire electric discharge machining is used for cutting excess metals of thin sheet metal parts. NC enables us to machine of complicated shapes. The thicknesses of heat-affected layers (: recast layers formed on surfaces in electric machining processes) are controlled. This ensures the processes are in high-quality.
FABLICATION
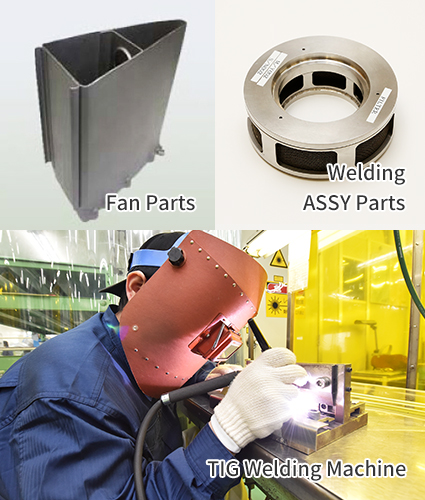
Welding
< Overview of Process >
Tungsten Inert Gas Arc Welding (TIG), Plasma Arc Welding, YAG Laser Welding, Resistance Welding
The process has NADCAP accreditation. The welders are capable of jointing thin sheet metal parts while minimizing welding distortion.
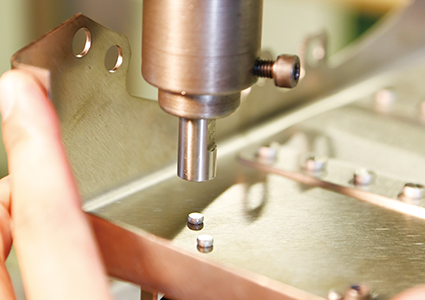
Rivet Process
In the rivet process, our company has a lot of experience , mainly for aerospace parts, and supplies parts to be mounted on space stations. With our deep experience and skills we have gained over time, our company provides products with stable and high-quality.
QUALITY ASSURANCE
Non Destructive Inspection (NDI)
Our company has a NDI system where NDI personnel and inspectors qualified in our qualification system established based on NAS-410.
< Overview of Inspection >
Fluorescent Penetrant Inspection (FPI)
Water Washable Fluorescent Penetrant Method [Normal/high sensitivity], Post Emulsifiable Fluorescent Penetrant Method [Super high sensitivity]
The inspection process has NADCAP accreditation.
The applicable specifications/standards: ASTM E 1417 and other customer requirements.
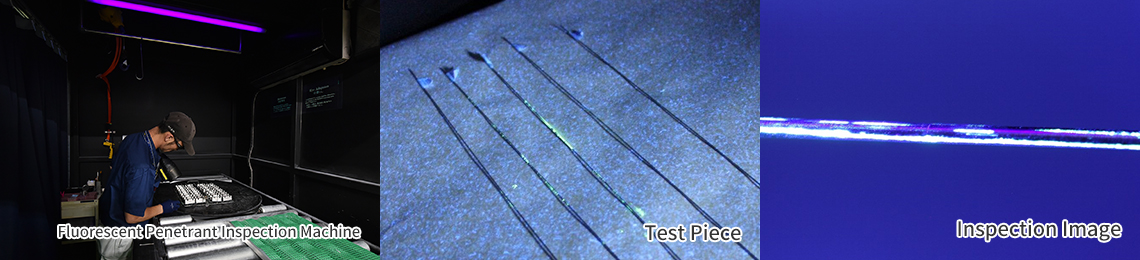
Magnetic Particle Inspection (MPI)
Fluorescent Magnetic Particle Inspection [Circular/Longitudinal magnetization methods], which detects surface and subsurface discontinuities on ferromagnetic materials.
The applicable specifications/standards: ASTM E 1444, and other customers’ requirements.
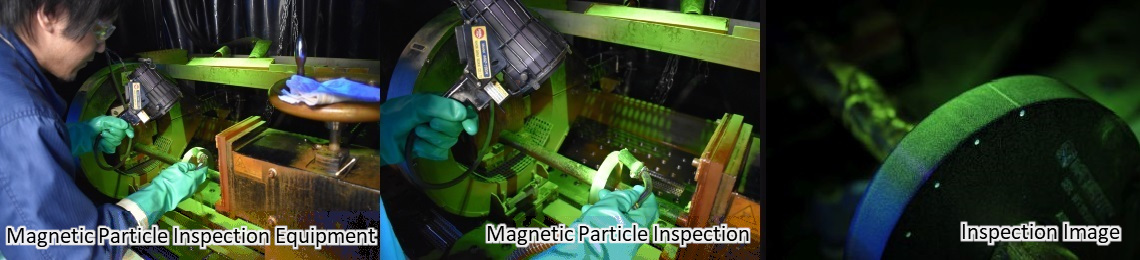
Radiography Inspection (RT)
Film Method: RT detects internal discontinues in weldments and castings.
The applicable specifications/standards: ASTM E 1742 and other customers’ requirements.
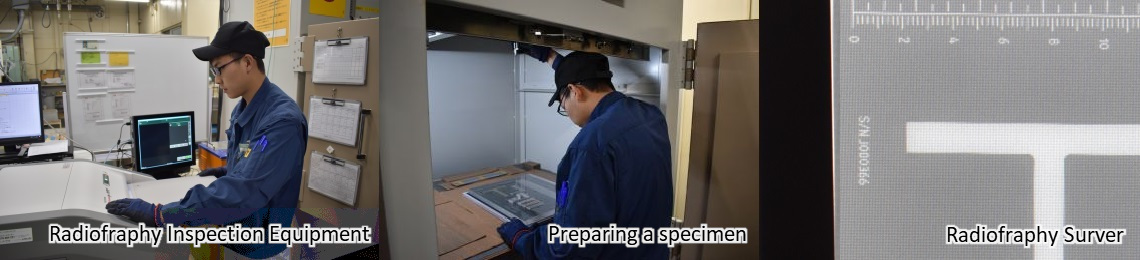
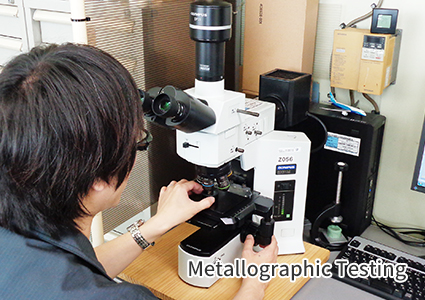
Material Testing (Captive Lab.)
The Lab. is capable of evaluation and analysis on our products after special processes, and has results of CLASS 1 in EXOVA/PTP every year. The Lab. offers metallographic/hardness testing required with customer certifications (IHI, S400, JAEC etc.), as well as tensileness/compression testing and chemical analysis and fracture analysis using SEM/EDX and EPMA, if necessary.
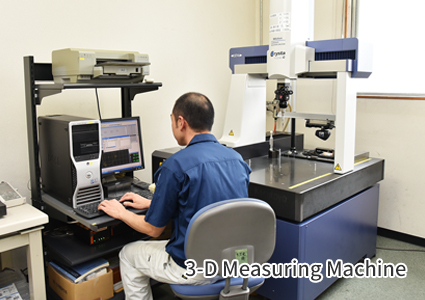
Inspection Measurement
There are normal measuring instruments, 3-D measuring machines, vision measuring system etc., which assure traceability to standards. Inspection using tools whose accuracy is assured is also available. The inspectors have their qualifications necessary under competence management.